Optimizing Kitting in Manufacturing – a How-To Guide for Customers providing Consigned kits
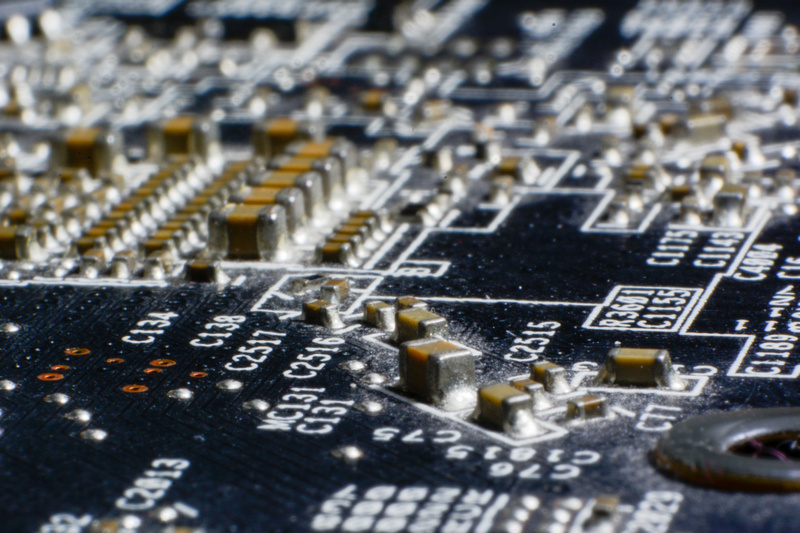
Become your Assembly House’s favorite customer by providing easy to audit kits
We see a variety of methods to provide parts in kits. Still, they usually involve supplying any parts required for a job within large cases with the parts individually packed in plastic bags or cardboard boxes.
The supply chain is being disrupted with shortages, logistics issues, and staffing. You have an opportunity to make a significant impact and help speed your product delivery by improving your kitting process. When your kit is audited quickly and accurately, it hits the production floor timely and moves through the shop at a much more rapid pace.
Delays?
Unfortunately, the “shoebox approach” to kitting often does not help us provide service excellence.
Delays can happen if a kit is delivered to your contract manufacturer with a plethora of random parts in a box, and the manufacturer has to dig through it.
The Shoe Box Approach
We see this regularly. It is incredibly time-consuming to send parts for more than one assembly, mixed in the same or multiple boxes. The Auditor is forced to dig through all boxes and allocate parts to everything simultaneously, without a packing slip that clearly denotes which parts go where; this exercise becomes exceptionally laborious and adds unneeded delays to the kit release time frame. The best practice for sending parts for multiple kits is to put parts for each assembly in its own box. If there are shared parts, please mark them clearly on your packing list and on the part itself.
Packing Lists are important
With a box that is missing a packing list, there are issues during the process before completion. It creates a communication breakdown: “you can’t be short that part; I know I put it in the box.” And your manufacturer will be challenged to give excellent service.
A packing list should include the basic identifying information for your job, such as customer name, PO number, assembly number/name, part numbers, and QTY.
Other information extremely valuable to the assembly house is:
Alternates: With component availability the way it is these days, we know to expect alternate parts. But if those alternates are not listed on your BOM or pack slip, we are left with a bag (or bags) of parts we can’t place. This requires us to give the questioned parts to your Program Manager, who must send an email, wait for a response, etc. You can see how this will add hours to an audit that could be completed quickly if the alternate was listed on the packing list.
Shared Parts: We understand that you may ask to share components between multiple kits. This is expected with parts on reels. However, we can work together to maximize efficiency when using this approach. Your Program Manager can help you develop an appropriate strategy to meet your specific needs. In general, if parts will be shared across multiple kits/assemblies, please make a note on pack slips. Let us know which box the part is in and which kit(s) it should go to. This is especially important if a shared part was already allocated to a kit that is in WIP on the production floor.
When you include a detailed pack slip, you can be assured your manufacturer will do a much better job auditing the kit and have a document to validate for shortages.
Overages
Did you know that the process of loading an SMT part onto a feeder requires the cover tape to be pulled back, exposing any parts that may be in those pockets? This means strips of parts without an empty leader will automatically lose 2-15 parts depending upon the part size and tape width. In general, the smaller the part and the thinner the tape, the more parts are lost. This loss is duplicated during the unloading process and can result in even higher quantities falling out depending upon the machine platform and feeder used. Out of the Box Manufacturing’s rule of thumb for overages is listed on every quote provided. When you provide sufficient overage, we save time by not waiting for shortages to be fulfilled and hand-added at the end of the run.
In Conclusion
We want to work with our customers to help speed their product delivery. An excellent kitting process ensures accuracy and timely delivery and allocates more turn time on the shop floor than in the warehouse.
It is more important than ever to evaluate potential delivery issues with the disrupted supply chain, shortages, logistics, and staffing issues. The kitting process is critical to ensuring timely and accurate delivery.
Do you have a project? Don’t hesitate to contact us or request a quote here.